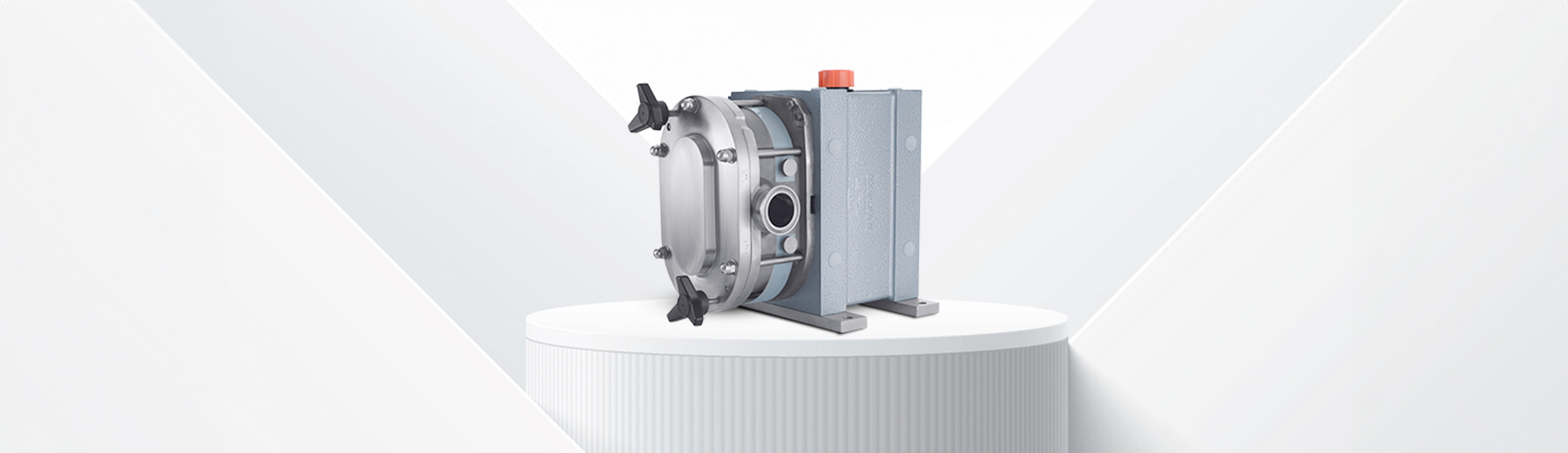
The food and beverage manufacturing industry requires high-pressure food processing pumps to maintain product quality, operational efficiency, as well as safety standards. Periodic pump maintenance has the additional benefit of not only extending the life of the equipment but also preventing costly downtimes of production.
But first just like any machine pump also needs maintenance for efficient performance. Failure to maintain pumps in good condition leads to a series of effects ranging from reduced productivity to increased food contamination and ultimately losses in the business.
Why Pump Maintenance Matters?
High-pressure food processing pumps can be used in pasteurization, homogenization, and transferring viscous fluids during food processing. These pumps are developed for operating in this industry but being machines they need maintenance for efficient performance.
The Importance of Pump Maintenance
- Ensures Consistent Product Quality: Maintained pumps ensure that there is uniformity in how products are processed and that the products conform to high standards of quality. When there is a failure in the performance of the pump then this will result in the production of inconsistent products which will contribute to consumer dissatisfaction and damage the brand image.
- Prevents Contamination: In the food and beverage industry, hygiene is of great importance. Routine maintenance can also help reduce the risk of leaks that may cause contamination. This applies especially to high-pressure pumps in industries such as pasteurization where the conditions must be sterile.
- Reduces Downtime: Unscheduled downtime can be extremely costly for manufacturers. Preventive maintenance also enables identifying possible failures before they occur and thus prevents unexpected stoppages and contributes to uninterrupted operation.
- Extends Equipment Life: Routine maintenance helps to extend the life of high-pressure food processing pumps from wear and tear. This can lead to significant cost-savings on replacements or major repairs.
- Compliance with Regulations: The food and beverage industry is subject to strict regulatory standards. Regular maintenance ensures that pumps operate within the required parameters, helping manufacturers comply with industry regulations and avoid penalties.
Maintenance Best Practices for Food & Beverage Pumps
- Schedule regular inspections: Develop a preventive maintenance schedule based on the pump's usage and the manufacturer's recommendations.
- Clean and Sanitize: Food-grade cleaning and sanitation procedures are crucial to maintain hygiene standards.
- Inspect Seals and Bearings: Regularly check seals and bearings for wear and tear to prevent leaks and ensure smooth operation.
- Lubricate as Needed: Proper lubrication reduces friction and wear on critical components, extending pump life.
- Invest in Training: Ensure your staff is trained on proper pump operation and maintenance procedures.
Real-World Example: Dairy Processing in India
Let's take an example of a dairy processing plant in rural Maharashtra. Here, high-pressure food processing pumps are operated in large numbers for pasteurization and homogenization. The plant also has a maintenance strategy for its pumps to maintain the consistent quality of the dairy products.
Major maintenance consists of weekly checks, monthly oiling and a quarterly clean of the pumps. Moreover, it uses a performance monitoring system to detect the condition of the pumps and rectify them before any failure. This preventative culture has also led to a decrease in downtime, increases in product quality, and adherence to food safety regulations. Thus increasing the overall business productivity.
Conclusion
Regular maintenance of high-pressure food processing pumps is essential for the success of food and beverage manufacturing operations. By ensuring consistent product quality, preventing contamination, reducing downtime, extending equipment life, and complying with regulations, proper pump maintenance can provide significant benefits to manufacturers.
For expert assistance in maintaining your high-pressure food processing pumps, contact Fristam Pumps (India) Pvt Ltd. Our comprehensive maintenance services and industry expertise can help ensure your pumps operate at peak performance, driving efficiency and quality in your manufacturing processes.
FAQs:
1) What is the importance of having maintenance on pumps?
Pump maintenance ensures food safety (prevents leaks, and contamination), optimizes performance (reduces energy costs, avoids breakdowns) and extends pump lifespan (saves money on replacements).
2) Why are pumps important in the food industry?
Food industry pumps are crucial for moving ingredients, maintaining hygiene (sanitation processes), and ensuring efficient production flow.
3) What are the common types of pumps used in food and beverage manufacturing?
Common food and beverage manufacturing pumps include:
- Positive displacement pumps (e.g., rotary lobe pumps) for handling thick liquids and pastes.
- Centrifugal pumps for efficient transfer of liquids like juices and beverages.
- Sanitary pumps are designed for easy cleaning and sterilization to meet hygiene standards.
4) What are the best practices for pump maintenance in the food and beverage industry?
Best practices for food & beverage pump maintenance include:
- Regular inspections and cleaning/sanitation.
- Checking seals and bearings for wear.
- Proper lubrication.
- Staff training on pump operation and maintenance.